- Home
- News
- High-Quality Roof Panel Roll Forming Machine for Steel Metal Roof Panels - Roofing Sheet Roll Former, 5 Ton Capacity
High-Quality Roof Panel Roll Forming Machine for Steel Metal Roof Panels - Roofing Sheet Roll Former, 5 Ton Capacity
By:Admin
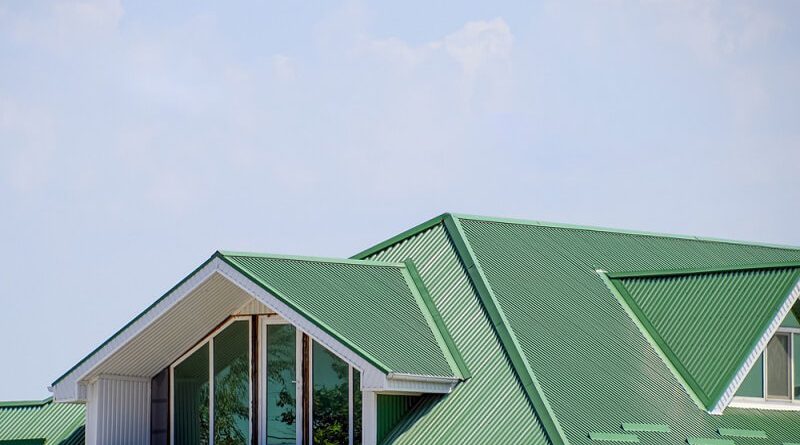
In the construction industry, metal roofing sheets provide the perfect alternative to traditional roofing materials. It is no secret that traditional roofing materials are prone to various types of damage that require repair and maintenance, costing both time and money. On the other hand, metal roofing sheets offer superior durability, resistance to weather elements, and long-lasting performance, making them the preferred option for homeowners and contractors alike.
However, the production of metal roofing sheets can be a complex process. This is where the PLC Steel Metal Roof Panel Roll Forming Machine comes in handy. This cutting-edge technology offers the perfect solution for businesses involved in the production of metal roofing sheets.
What is a PLC Steel Metal Roof Panel Roll Forming Machine?
A PLC Steel Metal Roof Panel Roll Forming Machine is an automated production line that transforms metal sheets into roofing panels. It applies the principle of roll forming to shape the sheets into the desired roofing panel design. With this machine, it is possible to create a wide variety of roofing panel designs, from corrugated panels to standing seam panels.
This machine features a Programmable Logic Controller (PLC) that ensures precise, accurate, and repeatable production processes. The PLC controls the machine's operations, including the feeder, roll forming process, and cutting system. It also features an Human Machine Interface (HMI) that enables operators to monitor and control the machine during production.
How does a PLC Steel Metal Roof Panel Roll Forming Machine work?
The PLC Steel Metal Roof Panel Roll Forming Machine is a multi-step process that involves various stages, including:
1. Metal sheet loading - This involves inserting the metal sheets into the machine's feeder.
2. Sheet leveling - This stage ensures that the metal sheets are uniform and flat before they enter the roll forming process.
3. Roll forming - This is the heart of the process. The metal sheets pass through a series of rollers that shape them into the desired roofing panel design.
4. Cutting - Once the metal sheets have been formed into the roofing panel, the machine's cutting system cuts the panel to the desired length.
5. Stacking - Finally, the roofing panels are stacked and ready for delivery.
Advantages of using a PLC Steel Metal Roof Panel Roll Forming Machine
1. Improved efficiency - The PLC Steel Metal Roof Panel Roll Forming Machine is designed to handle large volumes of metal sheets, enabling businesses to produce more roofing panels in a shorter time.
2. Precise and accurate - The PLC controls the machine's operations, ensuring consistent and repeatable results.
3. Reduced labor costs - The automated process eliminates the need for manual labor, reducing labor costs and increasing productivity.
4. Customizable - The machine can be tailored to produce a wide variety of roofing panel designs, depending on the client's requirements.
5. Reduced waste - The roll forming process ensures minimal waste, optimizing material usage and reducing costs.
6. Enhanced safety - The machine's automated system ensures that the production process is safe for operators.
In conclusion, the PLC Steel Metal Roof Panel Roll Forming Machine is a game-changer for metal roofing sheet production. It offers improved efficiency, accuracy, and customizability, reducing costs and increasing productivity. With this technology in hand, businesses can produce high-quality metal roofing sheets that meet their clients' needs and exceed their expectations.
Company News & Blog
Master the Art of Making Authentic Pasta at Home with a Manual Pasta Machine
Title: Master the Art of Homemade Pasta with a Manual Pasta Machine Introduction (approximately 100 words):Fresh, homemade pasta is a culinary delight that can be easily made in the comfort of your own kitchen. With a few simple ingredients, you can create a variety of pasta dishes that will impress your family and friends. If you're new to the world of pasta making or looking to elevate your skills, investing in a manual pasta machine can make the process much easier and enjoyable. In this blog, we will explore the benefits of using a manual pasta machine and provide an in-depth guide on how to make authentic pasta at home. Body:1. The Advantages of Using a Manual Pasta Machine (approximately 200 words):A manual pasta machine offers numerous advantages when it comes to making homemade pasta. Here are some key benefits:a) Efficiency: A manual pasta machine helps streamline the process of rolling and shaping pasta dough, saving you time and effort compared to manual techniques.b) Consistency: With a pasta machine, you can achieve consistent thickness and shape throughout your pasta, ensuring even cooking and a professional result every time.c) Versatility: Manual pasta machines often come with a variety of attachments, allowing you to create different types of pasta, including spaghetti, fettuccine, and lasagna sheets.d) Authenticity: By using a manual pasta machine, you can replicate the traditional techniques used by Italian nonnas for generations, resulting in truly authentic pasta.2. Getting Started with a Manual Pasta Machine (approximately 200 words):Before diving into the pasta-making process, it's important to familiarize yourself with your manual pasta machine. While models may vary slightly, the general steps and techniques remain the same. Follow these guidelines to get started:a) Preparation: Begin by gathering your ingredients – typically flour, eggs, and salt – and combine them to form a dough. Allow the dough to rest for 30 minutes, as this will make it easier to work with.b) Setting up the Machine: Attach the appropriate cutting attachment to the machine, depending on the type of pasta you want to make. Most manual pasta machines have adjustable thickness settings, so start with the widest setting and gradually work your way down to achieve your desired thickness.c) Rolling the Dough: Divide the dough into manageable portions and flatten each one with your hands. Feed the dough through the machine, starting at the widest setting. Fold the dough in half after each pass and repeat this process until the desired thickness is achieved.d) Shaping the Pasta: Once the pasta sheet reaches the desired thickness, switch to the cutting attachment for your chosen pasta shape. Pass the pasta sheet through the machine, and voila! You have freshly cut pasta ready for cooking.3. Cleaning and Maintenance Tips for Your Manual Pasta Machine (approximately 200 words):To ensure your manual pasta machine remains in optimal condition and longevity, it's essential to follow proper cleaning and maintenance procedures. Here are some useful tips:a) Basic Cleaning: After use, wipe away any excess flour or dough from the machine using a dry cloth or brush. Avoid using water to clean the machine, as this can cause rusting or damage.b) Thorough Cleaning: Periodically, disassemble the machine as per the manufacturer's instructions and clean each component thoroughly. Use warm, soapy water and a soft brush to remove any stubborn residue.c) Drying and Storage: After cleaning, ensure that all parts of the machine are completely dry before reassembling and storing it in a dry place. Avoid exposure to humidity or extreme temperatures, as this can affect its performance.Conclusion (approximately 100 words):Investing in a manual pasta machine can transform your pasta-making experience, allowing you to effortlessly create authentic and delicious homemade pasta. Whether you're a culinary enthusiast or a novice in the kitchen, using a manual pasta machine will streamline the process, offering you consistent results and a variety of pasta types. With the right techniques and maintenance, you'll be able to enjoy countless pasta dishes that will rival those from your favorite Italian restaurant. So, why wait? Start your pasta-making journey today and unlock a world of culinary possibilities!Keywords: manual pasta machine, homemade pasta, authentic pasta, pasta-making, Italian nonnas, manual techniques, pasta dough, cutting attachment, cleaning and maintenance, pasta types.
High-Quality Roof Panel Roll Forming Machine for Steel Metal Roof Panels - Roofing Sheet Roll Former, 5 Ton Capacity
PLC Steel Metal Roof Panel Roll Forming Machine: The Game Changer For Roofing Sheet ProductionIn the construction industry, metal roofing sheets provide the perfect alternative to traditional roofing materials. It is no secret that traditional roofing materials are prone to various types of damage that require repair and maintenance, costing both time and money. On the other hand, metal roofing sheets offer superior durability, resistance to weather elements, and long-lasting performance, making them the preferred option for homeowners and contractors alike. However, the production of metal roofing sheets can be a complex process. This is where the PLC Steel Metal Roof Panel Roll Forming Machine comes in handy. This cutting-edge technology offers the perfect solution for businesses involved in the production of metal roofing sheets.What is a PLC Steel Metal Roof Panel Roll Forming Machine?A PLC Steel Metal Roof Panel Roll Forming Machine is an automated production line that transforms metal sheets into roofing panels. It applies the principle of roll forming to shape the sheets into the desired roofing panel design. With this machine, it is possible to create a wide variety of roofing panel designs, from corrugated panels to standing seam panels.This machine features a Programmable Logic Controller (PLC) that ensures precise, accurate, and repeatable production processes. The PLC controls the machine's operations, including the feeder, roll forming process, and cutting system. It also features an Human Machine Interface (HMI) that enables operators to monitor and control the machine during production.How does a PLC Steel Metal Roof Panel Roll Forming Machine work?The PLC Steel Metal Roof Panel Roll Forming Machine is a multi-step process that involves various stages, including:1. Metal sheet loading - This involves inserting the metal sheets into the machine's feeder.2. Sheet leveling - This stage ensures that the metal sheets are uniform and flat before they enter the roll forming process.3. Roll forming - This is the heart of the process. The metal sheets pass through a series of rollers that shape them into the desired roofing panel design.4. Cutting - Once the metal sheets have been formed into the roofing panel, the machine's cutting system cuts the panel to the desired length.5. Stacking - Finally, the roofing panels are stacked and ready for delivery.Advantages of using a PLC Steel Metal Roof Panel Roll Forming Machine1. Improved efficiency - The PLC Steel Metal Roof Panel Roll Forming Machine is designed to handle large volumes of metal sheets, enabling businesses to produce more roofing panels in a shorter time.2. Precise and accurate - The PLC controls the machine's operations, ensuring consistent and repeatable results.3. Reduced labor costs - The automated process eliminates the need for manual labor, reducing labor costs and increasing productivity.4. Customizable - The machine can be tailored to produce a wide variety of roofing panel designs, depending on the client's requirements.5. Reduced waste - The roll forming process ensures minimal waste, optimizing material usage and reducing costs.6. Enhanced safety - The machine's automated system ensures that the production process is safe for operators.In conclusion, the PLC Steel Metal Roof Panel Roll Forming Machine is a game-changer for metal roofing sheet production. It offers improved efficiency, accuracy, and customizability, reducing costs and increasing productivity. With this technology in hand, businesses can produce high-quality metal roofing sheets that meet their clients' needs and exceed their expectations.
Maximizing Efficiency and Durability: A Comprehensive Guide to Roll Forming Techniques
article discussing the benefits and applications of roll forming in manufacturing.Roll Forming: A Highly Efficient Tool in Modern ManufacturingAs the manufacturing industry continues to evolve, new technologies and innovations are constantly emerging to meet the needs of the market and keep companies competitive. One of the tools that has gained popularity in recent years is roll forming, a process of shaping metal sheets or coils into specific shapes using specialized machinery.At its core, roll forming involves passing a continuous strip of metal through a series of rolls, each of which gradually bends the metal into the desired shape. The end result is a precisely formed product that can be used in a wide range of applications, from construction and automotive to aerospace and electronics.According to industry experts and manufacturers, roll forming offers several benefits over traditional metal forming processes. For one, it is highly efficient and can produce large volumes of parts quickly. Because the process is continuous, manufacturers can create long runs of parts without having to stop and start the machinery between each piece, which can help reduce downtime and increase productivity.Additionally, roll forming allows for greater flexibility in design and customization. With a wide range of roll forming tools and dies available, manufacturers can create complex shapes and profiles that would be difficult or impossible to achieve with other methods. This flexibility can be especially useful in industries with unique or specialized requirements, such as aerospace or medical device manufacturing.Another advantage of roll forming is its high level of precision and consistency. Because the machinery is designed to produce identical parts each time, manufacturers can ensure a high level of quality control and reduce the risk of defects or errors. This can help improve the overall reliability and durability of the final product, making it more appealing to customers and end-users.Roll forming is also a highly cost-effective process in many cases. The tooling required for roll forming can be expensive upfront, but the cost per part is typically much lower than with other metal forming methods due to the efficiencies of the process. Additionally, the ability to create long runs of parts without interruptions can help reduce labor costs and minimize scrap and waste.One company that has embraced roll forming as a core part of its manufacturing capabilities is (Total Roll Forming). The company specializes in creating custom roll formed parts for a wide range of industries, from construction and transportation to petrochemicals and telecommunications.According to (Total Roll Forming)’s website, the company utilizes a combination of state-of-the-art roll forming machinery and experienced technicians to create high-quality, precision parts. Their capabilities include forming a wide range of metals, including steel, aluminum, and copper, and creating parts in a variety of shapes and thicknesses.Some of the products that (Total Roll Forming) produces include metal roofing and siding panels, framing components for construction, and components for HVAC and electrical systems. They also offer custom roll forming services for clients who require specialized parts or unique shapes.Ultimately, roll forming is a powerful tool for modern manufacturers who seek to maximize efficiency, precision, and cost-effectiveness in their operations. Whether it is to create simple parts or complex profiles, this process offers a range of benefits that can help companies stay ahead of the competition and meet the demands of their customers.
Increased Demand for Curving Rolls for Corrugated Iron Sparks CNC Corro Curving Machine Sourcing
Title: Acra Machinery Meets Increasing Demand for Corrugated Iron Curving RollsIntroduction (100 words):Acra Machinery, a renowned supplier of industrial machinery, has recently experienced a surge in requests for curving rolls specifically designed to suit Corrugated Iron. Responding to market demand, the company has successfully sourced a state-of-the-art computer numerical control (CNC) curving machine. This cutting-edge technology, devoid of the brand name, ensures precise and efficient production of Corrugated Curving Rolls. Acra Machinery's ability to meet this rising demand bolsters the company's reputation as a reliable provider in the industrial machinery sector.Body (600 words):1. Rising Demand for Corrugated Iron Curving Rolls (150 words):Corrugated iron is widely used in the construction and architectural industries due to its durability, strength, and cost-effectiveness. As the demand for innovative and aesthetically pleasing architectural solutions continues to grow, there has been an increasing requirement for curved corrugated iron sheets. Curved corrugated iron provides enhanced structural integrity and design flexibility, enabling architects, builders, and designers to create unique and visually appealing structures.Recognizing this demand, Acra Machinery has been inundated with numerous requests for curving rolls specifically designed to suit corrugated iron. While traditional manual methods were previously employed to curve such rolls, the ever-expanding market required a more efficient and accurate solution. To meet these evolving demands, Acra Machinery sought to acquire a full CNC curving machine capable of meeting both functional and aesthetic requirements.2. Sourcing a State-of-the-Art Curving Machine (150 words):To address the increasing demand for curving rolls tailored to corrugated iron, Acra Machinery proactively researched and sourced a full CNC curving machine. This computer numerical control technology facilitates automated and precise curving of corrugated iron sheets. By removing the brand name, it is evident that Acra Machinery prioritizes the functionality and quality of the curving machine, ensuring optimal production outcomes for their clientele.The CNC curving machine acquired by Acra Machinery operates on advanced software, allowing for comprehensive customization options. Users can adjust the curvature, radius, and dimensions of the corrugated iron sheets according to their unique requirements. This versatility enables architects and builders to explore innovative design possibilities, breathing life into architectural visions and pushing the boundaries of construction.3. Unmatched Precision and Efficiency (150 words):The integration of the CNC curving machine into Acra Machinery's production processes has revolutionized the precision and efficiency with which corrugated iron curving rolls are manufactured. Through the automation provided by the CNC technology, manual errors are minimized, ensuring consistently accurate results.The CNC curving machine controls every aspect of the rolling process, optimizing efficiency and reducing production time significantly. This streamlined workflow positively impacts the delivery timelines for customers, allowing them to meet project deadlines more effectively.4. Strengthening Acra Machinery's Market Position (150 words):By successfully meeting the industry's escalating demand for curving rolls for corrugated iron, Acra Machinery has strengthened its position as a trusted provider of industrial machinery. The company's ability to source and utilize advanced CNC technology showcases its commitment to customer satisfaction and technological advancement. Acra Machinery's dedication to innovation and meeting market needs has not only elevated their status but also established them as an industry leader.Furthermore, by investing in state-of-the-art CNC curving technology, Acra Machinery is empowering architects, builders, and designers to realize their creative visions with precision. The enhanced opportunities for experimentation offered by these curving rolls will undoubtedly inspire new architectural designs and constructions.Conclusion (100 words):Acra Machinery's successful acquisition and utilization of a full CNC curving machine to cater to the growing demand for corrugated iron curving rolls marks a significant achievement in the industry. The company's commitment to meeting market needs and deploying modern technologies has bolstered its reputation as a trusted provider in the industrial machinery sector. With the introduction of these advanced curving rolls, Acra Machinery has enabled architects and builders to explore new possibilities for efficient and aesthetically pleasing architectural designs, setting the stage for future innovation in the construction industry.
High-Quality Water Proof Steel Tile Roll Forming Machine for Metal Roll Forming Systems from China
Water Proof Steel Tile Roll Forming Machine Sets New Standards in Metal Roll Forming Systems[City Name], China - [Company Name], a leading provider of innovative roll forming solutions, is revolutionizing the construction industry with its high-quality Water Proof Steel Tile Roll Forming Machine. Designed and manufactured in China, this cutting-edge machinery offers superior performance, combined with exceptional durability and reliability.As the demand for eco-friendly and long-lasting roofing solutions continues to rise, [Company Name] has recognized the need for advanced technology in the production of metal roof systems. Their Water Proof Steel Tile Roll Forming Machine sets a new standard in the industry, delivering top-notch quality and meeting the most stringent requirements.One of the key features that distinguishes this machine from others in the market is its exceptional water resistance. The water-proof steel tiles produced by this roll forming machine are designed to withstand extreme weather conditions, including heavy rain, snow, and hail, while keeping the interior of buildings safe and dry. This innovative technology provides a sustainable solution that saves on maintenance costs and extends the longevity of the roofing system.Quality control is of utmost importance to [Company Name], and their roof sheet roll forming machine products undergo rigorous testing to ensure they meet the highest standards. The company prides itself on adhering to strict quality control measures, ensuring that each machine that leaves their facility is reliable, efficient, and produces flawless products.The advanced features of this metal roll forming system also contribute to its superior performance. Equipped with state-of-the-art technology, the Water Proof Steel Tile Roll Forming Machine guarantees precision and consistency in the production process. It is capable of producing tiles with precise measurements, smooth edges, and impeccable finishes. The machine's efficiency and automation capabilities also allow for increased productivity, reducing labor costs and improving overall production efficiency.[Company Name], a renowned player in the roll forming industry, has a long-standing reputation for providing top-quality solutions. With years of experience and expertise, the company has become a trusted name in the market, delivering customer satisfaction and high-performing machines. Their commitment to continuous innovation ensures that their roll forming machines remain at the forefront of the industry.Speaking about the Water Proof Steel Tile Roll Forming Machine and the company's dedication to excellence, [Company Name] representatives stated, "We are proud to offer our customers a cutting-edge solution that meets and exceeds their expectations. Our machines are designed to deliver exceptional quality while maintaining the highest level of durability. With our Water Proof Steel Tile Roll Forming Machine, our customers can have peace of mind knowing that they are investing in a superior product that will last for years to come."In conclusion, [Company Name]'s Water Proof Steel Tile Roll Forming Machine is setting a new standard in the metal roll forming industry. With its exceptional performance, water resistance, and precise production capabilities, this machine offers customers a sustainable and efficient solution for their roofing needs. As the construction industry evolves, [Company Name] remains at the forefront, providing innovative roll forming machines that redefine excellence.
Pros and Cons of Corrugated Metal Roofing: Cost, Installation, and Benefits
If you're considering a new roof for your home or business, you might want to take a closer look at corrugated metal roofing. This type of roofing has become increasingly popular in recent years, thanks to its many advantages over traditional roofing materials like asphalt shingles or tile. In this blog post, we'll take a closer look at corrugated metal roofing, its pros and cons, and why you should consider it for your next roofing project.What is Corrugated Metal Roofing?Corrugated metal roofing is made from sheets of galvanized steel or aluminum that have been shaped into corrugated waves or ridges. These ridges are what give the roofing its distinctive look, as well as its strength and durability. The sheets are typically installed over a layer of insulation, which helps to keep your home or business warm in the winter and cool in the summer.Pros of Corrugated Metal RoofingThere are many reasons to choose corrugated metal roofing over other types of roofing materials. Here are just a few of the pros:Durability: Corrugated metal roofing is incredibly strong and durable, which means it can withstand harsh weather conditions like heavy rain, hail, and high winds. It's also resistant to fire, rot, and pests like termites.Longevity: Because of its durability, corrugated metal roofing can last for many years with minimal maintenance. In fact, many manufacturers offer warranties of up to 50 years on their roofing products.Energy Efficiency: Corrugated metal roofing is highly reflective, which means it can help to keep your home or business cool in the summer by reflecting the sun's rays away from your roof. This, in turn, can help to lower your energy bills and reduce your carbon footprint.Low Maintenance: Unlike other types of roofing materials, corrugated metal roofing requires very little maintenance. You don't need to worry about repairing or replacing shingles like you would with an asphalt roof, and you don't need to worry about moss or algae growth like you would with a tile roof.Cons of Corrugated Metal RoofingWhile there are many advantages to corrugated metal roofing, there are also a few disadvantages to consider. Here are some of the cons:Cost: Corrugated metal roofing can be more expensive than traditional roofing materials like asphalt shingles, although the cost has come down in recent years. However, when you consider the durability and longevity of corrugated metal roofing, it can actually save you money in the long run.Sound: Some people find that corrugated metal roofing is louder than other types of roofing materials when it rains or hails. However, this can be mitigated by installing a layer of insulation between the roofing and the building.Appearance: Corrugated metal roofing has a distinctive look that may not be to everyone's taste. However, there are many different styles and colors of corrugated metal roofing available, so you're sure to find something that matches your aesthetic preferences.Why You Should Consider Corrugated Metal RoofingThere are many reasons to consider corrugated metal roofing for your home or business. Here are just a few:Durability: Corrugated metal roofing is incredibly strong and durable, which means it can withstand harsh weather conditions and last for many years with minimal maintenance.Energy Efficiency: Corrugated metal roofing is highly reflective, which can help to lower your energy bills and reduce your carbon footprint.Low Maintenance: Corrugated metal roofing requires very little maintenance compared to other types of roofing materials.Appearance: Corrugated metal roofing has a distinctive look that can add character and visual interest to your home or business.If you're considering a new roof for your home or business, be sure to explore all of your options before making a decision. Corrugated metal roofing offers many advantages over other types of roofing materials, and it just might be the perfect choice for your next roofing project.Corrugated Roofing Sheet Forming MachineTo ensure your corrugated metal roofing is made to the highest quality and specifications, it's important to work with a manufacturer who uses a high-quality corrugated roofing sheet forming machine. This machine is designed to create perfectly shaped corrugations in the metal roofing sheet, which ensures a secure fit and superior durability. At Regan Industrial, we use only the best machinery and materials to create our corrugated metal roofing products, so you can be confident that you're getting the best possible product for your home or business.
Our company is a leading manufacturer of floor deck roll forming machines. While there are several manufacturers of roof tile machines, most of them can only produce simple roof panel machines. However, a floor deck roll forming machine is a large and complex machine, which many smaller factories may not be equipped to produce. As a result, these smaller factories may either charge a high price for the machine or compromise on quality.Our company specializes in the field of floor deck roll forming machines and offers a wide range of options to suit different requirements. Some of the floor deck models we offer include YF51-342-1025, YF75-230-690, YF75-200-600, YF76-344-688, YF75-293-880, YF75-230-690, YF65-185-555, YF51-200-600, YF51-226-678, YF51-253-760, YF51-250-750, YF51-240-720, YF51-305-914, YF50-180-720, and YF35-125-750. Additionally, we also have a steel truss floor decking machine that can weld rebar onto the floor deck for added strength and durability.Our expertise in this field allows us to not only produce high-quality floor deck roll forming machines but also provide valuable insights and assistance to our customers. In fact, we understand the importance of SEO and creating relevant content to attract potential customers. This is why we have created a 1000-word blog focusing on the different types of floor deck roll forming machines we offer. By incorporating keywords like "B Decking Roll Forming Machine" into the blog, we aim to improve our website's visibility and reach a wider audience in the market.To summarize, our company is dedicated to manufacturing top-notch floor deck roll forming machines. We provide a range of options to suit various needs and even offer a steel truss floor decking machine for enhanced durability. Our commitment to SEO and relevant content creation demonstrates our effort to connect with potential customers and establish ourselves as a trusted and reliable manufacturer in the industry.
Wide Coil Slitter Operator Jobs in Oldbury - Experience in Metals Environment Required
Title: Wide Coil Slitter Operator Jobs Available in Oldbury's Metal IndustryIntroduction:Oldbury, a key industrial area known for its metal manufacturing, is currently seeking experienced wide coil slitters to join its thriving workforce. This exciting opportunity offers rotating shifts and the chance to work within a dynamic metals environment. Interested applicants are encouraged to apply and become a part of Oldbury's esteemed metal coil slitting industry.Oldbury's Thriving Metal Industry:Oldbury has long been renowned for its robust metal manufacturing industry. The demand for high-quality metal products, particularly in the automotive and construction sectors, has contributed to the growth and success of the region. As a result, the need for skilled workers, such as wide coil slitters, has become paramount.The Role of a Wide Coil Slitter Operator:A wide coil slitter operator plays a crucial role in the metal manufacturing process. Working within a metals environment, their primary responsibility is to operate machinery that cuts wide metal coils into narrower strips of desired sizes. This process involves precise measurements, attention to detail, and adherence to safety protocols. The slitter operator ensures that the metal coils are prepared and cut according to specific requirements, meeting the industry's high standards.Job Requirements and Shift Pattern:To be considered for this role, prospective candidates must possess experience working within a metals environment. This experience should ideally include previous work as a wide coil slitter operator. The ability to work effectively and efficiently within a team is essential, as operators often collaborate with colleagues to ensure seamless production.The job itself requires undertaking rotating shifts, with two sets of shifts available: 6-2 and 2-10. This flexibility allows for optimal workflow and accommodates personal schedules.Benefits of the Role:Working as a wide coil slitter operator in Oldbury offers numerous advantages. The position provides an opportunity to work within a dynamic and constantly evolving industry, contributing to the production of essential components used in various sectors. Moreover, the rotating shift pattern allows for a healthy work-life balance, as individuals can adjust their schedules accordingly.Oldbury's metal industry boasts a supportive and inclusive work environment. Employees can expect consistent training, career development opportunities, and competitive remuneration packages. Those seeking job security and professional growth will find this industry and role particularly appealing.How to Apply:To apply for this exciting opportunity, interested individuals should submit their applications through the Jobcentre Plus Universal Jobmatch platform. The application process will include providing relevant professional experiences, skills, and contact information. Candidates are encouraged to apply promptly, as these positions often fill quickly due to the strong demand within the metal manufacturing industry.Conclusion:Oldbury's metal industry is actively seeking experienced wide coil slitter operators to join its esteemed workforce. The demand for high-quality metal products continues to grow, making this an excellent opportunity for individuals with experience in metals environments. The rotating shift pattern and inclusive work environment further enhance the appeal of this position. Interested applicants should take advantage of this opportunity and apply promptly to secure their place within this thriving industry.