Wide Coil Slitter Operator Jobs in Oldbury - Experience in Metals Environment Required
By:Admin
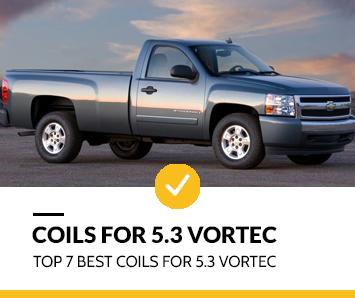
Introduction:
Oldbury, a key industrial area known for its metal manufacturing, is currently seeking experienced wide coil slitters to join its thriving workforce. This exciting opportunity offers rotating shifts and the chance to work within a dynamic metals environment. Interested applicants are encouraged to apply and become a part of Oldbury's esteemed metal coil slitting industry.
Oldbury's Thriving Metal Industry:
Oldbury has long been renowned for its robust metal manufacturing industry. The demand for high-quality metal products, particularly in the automotive and construction sectors, has contributed to the growth and success of the region. As a result, the need for skilled workers, such as wide coil slitters, has become paramount.
The Role of a Wide Coil Slitter Operator:
A wide coil slitter operator plays a crucial role in the metal manufacturing process. Working within a metals environment, their primary responsibility is to operate machinery that cuts wide metal coils into narrower strips of desired sizes. This process involves precise measurements, attention to detail, and adherence to safety protocols. The slitter operator ensures that the metal coils are prepared and cut according to specific requirements, meeting the industry's high standards.
Job Requirements and Shift Pattern:
To be considered for this role, prospective candidates must possess experience working within a metals environment. This experience should ideally include previous work as a wide coil slitter operator. The ability to work effectively and efficiently within a team is essential, as operators often collaborate with colleagues to ensure seamless production.
The job itself requires undertaking rotating shifts, with two sets of shifts available: 6-2 and 2-10. This flexibility allows for optimal workflow and accommodates personal schedules.
Benefits of the Role:
Working as a wide coil slitter operator in Oldbury offers numerous advantages. The position provides an opportunity to work within a dynamic and constantly evolving industry, contributing to the production of essential components used in various sectors. Moreover, the rotating shift pattern allows for a healthy work-life balance, as individuals can adjust their schedules accordingly.
Oldbury's metal industry boasts a supportive and inclusive work environment. Employees can expect consistent training, career development opportunities, and competitive remuneration packages. Those seeking job security and professional growth will find this industry and role particularly appealing.
How to Apply:
To apply for this exciting opportunity, interested individuals should submit their applications through the Jobcentre Plus Universal Jobmatch platform. The application process will include providing relevant professional experiences, skills, and contact information. Candidates are encouraged to apply promptly, as these positions often fill quickly due to the strong demand within the metal manufacturing industry.
Conclusion:
Oldbury's metal industry is actively seeking experienced wide coil slitter operators to join its esteemed workforce. The demand for high-quality metal products continues to grow, making this an excellent opportunity for individuals with experience in metals environments. The rotating shift pattern and inclusive work environment further enhance the appeal of this position. Interested applicants should take advantage of this opportunity and apply promptly to secure their place within this thriving industry.
Company News & Blog
Premium Steel Sheets: Cut-to-Length, Shear and Slitter Cut Services at Unbeatable Prices!
Title: Enhance Your Project's Efficiency and Quality with Hot Rolled Slitter Steel SheetsIntroductionIn today's fast-paced construction and manufacturing industries, the demand for high-quality steel sheets that can be customized to specific requirements is at an all-time high. Hot rolled steel sheets have become an exceptionally popular choice due to their durability and versatility.This blog aims to shed light on the benefits and applications of hot rolled steel sheets and the key role played by slitter cutting services in meeting the varied needs of different projects. So, let's delve deeper into the world of hot rolled slitter steel sheets!Understanding Hot Rolled Steel SheetsHot rolled steel sheets are produced through a process involving heating steel slabs above their recrystallization temperature, followed by cooling them to room temperature. This technique results in a flexible, strong, and malleable steel product that can be further processed to various specifications. The hot rolling process eliminates impurities, while the controlled cooling ensures uniformity and consistency in the sheet's strength.Applications and Advantages1. Versatility: One of the primary benefits of hot rolled steel sheets lies in their versatility. From automotive manufacturing and construction to machinery fabrication and shipbuilding, these sheets find application across a wide range of industries. Their strength and malleability allow for seamless forming and shaping, making them suitable for diverse projects.2. Durability: Hot rolled steel sheets are known for their exceptional durability. They can withstand heavy loads, extreme temperatures, and harsh environments, ensuring a longer lifespan for your projects. Whether it's a structural application or a component in heavy machinery, hot rolled steel sheets provide the necessary strength and resilience.3. Cost-effectiveness: With their cost-effective production process, hot rolled steel sheets offer excellent value for money. Affordable and readily available, they are a preferred choice for projects that demand a high-volume supply of steel sheets without compromising on quality.The Role of Slitter Cutting ServicesTo maximize the benefits of hot rolled steel sheets, slitter cutting services come into play. Slitter cut refers to the process of cutting wide coils of steel into narrower strips, catering to specific project requirements. This technique ensures precision and accuracy, ensuring that the sheets are tailored to the desired dimensions.Importance of Slitter Cutting1. Customization: Slitter cutting enables customization by accommodating different project needs. Sheets can be cut into a variety of widths, lengths, and thicknesses, ensuring an exact fit for your project requirements. This flexibility eliminates the need for additional processing and minimizes waste, thereby optimizing overall efficiency and cost-effectiveness.2. Simplicity and Time Efficiency: Slitter cutting services streamline the manufacturing process by providing ready-to-use steel strips. This eliminates the need for additional cutting and reduces the time and effort spent in modifying the sheets on-site. Better time management and enhanced simplicity contribute to meeting project deadlines and improving overall work efficiency.3. Precision and Quality: Slitter cutting techniques ensure precise and accurate cuts, resulting in high-quality steel strips. The accurate dimensions obtained through slitter cutting services reduce the risk of errors and ensure a perfect fit for your project's requirements. This level of precision translates into improved structural integrity and better overall performance.ConclusionHot rolled slitter steel sheets offer a range of benefits that meet the demands of various industries. Their versatility, durability, and cost-effectiveness make them an ideal choice for your projects. By employing slitter cutting services, you can further enhance the efficiency and quality of your projects. Customization, time efficiency, and precision are some of the significant advantages that slitter cutting brings to the table.When sourcing steel sheets, consider partnering with a reliable supplier offering hot rolled slitter steel sheets. By doing so, you can rest assured that you will receive quality products that are tailored to your exact requirements. Remember, investing in high-quality materials and services ensures the success and longevity of your projects in the long run.So, why wait? Embrace the versatility and reliability of hot rolled slitter steel sheets for your next construction or manufacturing project, and witness the remarkable difference it can make!
Maximizing Efficiency and Durability: A Comprehensive Guide to Roll Forming Techniques
article discussing the benefits and applications of roll forming in manufacturing.Roll Forming: A Highly Efficient Tool in Modern ManufacturingAs the manufacturing industry continues to evolve, new technologies and innovations are constantly emerging to meet the needs of the market and keep companies competitive. One of the tools that has gained popularity in recent years is roll forming, a process of shaping metal sheets or coils into specific shapes using specialized machinery.At its core, roll forming involves passing a continuous strip of metal through a series of rolls, each of which gradually bends the metal into the desired shape. The end result is a precisely formed product that can be used in a wide range of applications, from construction and automotive to aerospace and electronics.According to industry experts and manufacturers, roll forming offers several benefits over traditional metal forming processes. For one, it is highly efficient and can produce large volumes of parts quickly. Because the process is continuous, manufacturers can create long runs of parts without having to stop and start the machinery between each piece, which can help reduce downtime and increase productivity.Additionally, roll forming allows for greater flexibility in design and customization. With a wide range of roll forming tools and dies available, manufacturers can create complex shapes and profiles that would be difficult or impossible to achieve with other methods. This flexibility can be especially useful in industries with unique or specialized requirements, such as aerospace or medical device manufacturing.Another advantage of roll forming is its high level of precision and consistency. Because the machinery is designed to produce identical parts each time, manufacturers can ensure a high level of quality control and reduce the risk of defects or errors. This can help improve the overall reliability and durability of the final product, making it more appealing to customers and end-users.Roll forming is also a highly cost-effective process in many cases. The tooling required for roll forming can be expensive upfront, but the cost per part is typically much lower than with other metal forming methods due to the efficiencies of the process. Additionally, the ability to create long runs of parts without interruptions can help reduce labor costs and minimize scrap and waste.One company that has embraced roll forming as a core part of its manufacturing capabilities is (Total Roll Forming). The company specializes in creating custom roll formed parts for a wide range of industries, from construction and transportation to petrochemicals and telecommunications.According to (Total Roll Forming)’s website, the company utilizes a combination of state-of-the-art roll forming machinery and experienced technicians to create high-quality, precision parts. Their capabilities include forming a wide range of metals, including steel, aluminum, and copper, and creating parts in a variety of shapes and thicknesses.Some of the products that (Total Roll Forming) produces include metal roofing and siding panels, framing components for construction, and components for HVAC and electrical systems. They also offer custom roll forming services for clients who require specialized parts or unique shapes.Ultimately, roll forming is a powerful tool for modern manufacturers who seek to maximize efficiency, precision, and cost-effectiveness in their operations. Whether it is to create simple parts or complex profiles, this process offers a range of benefits that can help companies stay ahead of the competition and meet the demands of their customers.
Title: Discover the Ultimate Roof Sheet Rolling Machine for Your Roofing ProjectIntroduction:In today's competitive construction industry, it's essential to invest in the right tools and equipment to ensure the success of your projects. One crucial aspect of any roofing project is the roof sheet rolling machine, also known as the roof panel forming machine or roof panel roll forming machine. This advanced machinery plays a vital role in creating high-quality and durable roof sheets that are an integral part of any structure. In this blog, we will explore the significance of a roof sheet rolling machine and why finding the perfect one is essential. Additionally, we will discuss the leading manufacturers in China and their superior roof sheet rolling machine models available in the market.Understanding the Importance of a Roof Sheet Rolling Machine:A roof sheet rolling machine is specifically designed to transform raw metal sheets into precisely shaped and sized roof panels. This process involves a series of intricate stages, including material loading, roll forming, cutting, and product stacking. By using a roof sheet rolling machine, construction professionals can streamline the production process, ensuring accuracy, efficiency, and consistency.Benefits of Using a High-Quality Roof Sheet Rolling Machine:Investing in a high-quality roof sheet rolling machine offers numerous advantages for contractors and construction firms:1. Superior Durability: Top-notch machines are manufactured using premium-grade materials and components, ensuring the longevity and resilience of the equipment.2. Precision and Efficiency: Advanced technology and design features allow for precise panel forming, cutting, and sizing, minimizing material waste and increasing productivity.3. Versatility: Leading roof sheet rolling machines can produce a variety of different panel designs, enabling contractors to cater to diverse customer requirements.4. Easy Operation and Maintenance: Quality machines come with user-friendly interfaces, making them easy to operate. Moreover, maintenance requirements are minimal, reducing downtime during the production process.5. Output Quality: The use of reliable roof sheet rolling machines ensures consistent and uniform panel quality, giving clients peace of mind regarding the structural integrity of their roofs.Leading Manufacturers of Roof Sheet Rolling Machines in China:China has established itself as a global leader in manufacturing top-quality roof sheet rolling machines. Some renowned Chinese manufacturers that provide exceptional machines include:1. [Manufacturer 1]: Known for their commitment to superior design and engineering, this manufacturer offers a range of high-performance roof sheet rolling machines suitable for various roofing applications.2. [Manufacturer 2]: With a reputation built on innovation and precision engineering, this manufacturer produces advanced roof panel forming machines that promise remarkable accuracy, durability, and efficiency.3. [Manufacturer 3]: Known for their wide range of roll forming machinery, this manufacturer delivers top-quality roof panel roll forming machines that cater to the diverse needs of construction professionals.Conclusion:Investing in a roof sheet rolling machine is a game-changer for construction firms looking to enhance their roofing projects' efficiency, accuracy, and overall quality. The significance of finding a reliable and high-quality machine cannot be overstated. Manufacturers in China, such as [Manufacturer 1], [Manufacturer 2], and [Manufacturer 3], offer exceptional options that guarantee superior performance and durability. By choosing the right roof sheet rolling machine, you can elevate your roofing projects to new heights, ensuring customer satisfaction and success in your construction endeavors.Keywords: Roof Sheet Rolling Machine, Roof Panel Forming Machine, Roof Panel Roll Forming Machine
Metal Roofing Machines: A Guide for Contractors Looking to Purchase
article about the benefits of metal roofing machines for contractors.Metal roofing has been gaining popularity in recent years due to its durability, longevity, and eco-friendliness. As a contractor, the decision to invest in metal roofing machines is an important one, as it can greatly improve the efficiency and quality of your work. Metal roofing machines are specialized tools designed specifically for fabricating metal roofing panels and accessories, such as flashings and gutters. Here are some of the benefits of investing in metal roofing machines:EfficiencyOne of the biggest advantages of metal roofing machines is their ability to improve the efficiency of your work. With a metal roofing machine, you can quickly and easily fabricate custom panels and accessories on site, without having to rely on third-party suppliers or manufacturers. This saves time and greatly reduces the lead times associated with traditional metal roofing materials.VersatilityMetal roofing machines are incredibly versatile, and can be used to fabricate a wide range of roofing panels, including standing seam, corrugated, and tile profiles. This allows contractors to offer more options to their customers, and to tailor their solutions to the specific requirements of each project.QualityMetal roofing machines can greatly improve the quality of your work, as they are designed to produce consistent, high-quality panels and accessories. This means that you can ensure that every panel and accessory meets your exact specifications, and that you can achieve a level of precision and accuracy that is difficult to achieve with traditional roofing materials.Cost-effectivenessWhile the initial investment in metal roofing machines may seem steep, they can actually be a highly cost-effective solution for contractors. Since you can fabricate your own panels and accessories on site, you can greatly reduce your reliance on third-party suppliers, which can lower your material costs and increase your profit margins. Additionally, metal roofing machines are designed for durability and longevity, which means that they can provide a good return on investment over time.Eco-friendlinessMetal roofing machines are an eco-friendly solution for contractors, as they allow you to manufacture your own roofing panels and accessories on site, rather than relying on materials that have to be transported long distances. Additionally, metal roofing is a highly sustainable and recyclable material, which means that it is good for the environment.Company Introduction: Metal Roofing MachinesIf you are a contractor interested in investing in metal roofing machines, Metal Roofing Machines is a leading provider of high-quality, durable, and versatile machines for fabricating metal roofing panels and accessories. Our machines are designed and built to the highest standards, using the latest technology and materials. We offer a wide range of machines to suit the requirements of any project, from standing seam and corrugated panel machines to gutter machines and trim machines.At Metal Roofing Machines, we pride ourselves on our commitment to quality, reliability, and customer satisfaction. We understand the challenges that contractors face in the roofing industry, and we are dedicated to providing them with the tools and support they need to succeed. Whether you are a seasoned roofing contractor or just starting out in the industry, we have the expertise and experience to help you take your roofing business to the next level.ConclusionInvesting in metal roofing machines is a smart choice for contractors looking to improve the efficiency, quality, and sustainability of their work. With the right machines and the right support, you can take your roofing business to the next level and offer your customers the best possible solutions for their roofing needs. If you are interested in learning more about metal roofing machines and how they can benefit your business, contact Metal Roofing Machines today and speak to one of our experts.
Competitive Intelligence by Key Players in the Automatic Roll Forming Machine Market: Global Market Analysis and Size
Automatic Roll Forming Machine Market: Increasing Industrialization Driving Demand for C/Z Purlin Roll Forming MachinesThe global Automatic Roll Forming Machine market is expected to witness robust growth in the coming years, driven by increasing industrialization across the globe. The Automatic Roll Forming Machine is a highly versatile equipment that is used in industries such as construction, automotive, electronics, and aerospace, among others. It is used for forming metal sheets and strips into different shapes and sizes. Among the various types of Roll Forming Machines, C/Z Purlin Roll Forming Machine is a popular choice for manufacturing structures that require strong supports for roofing, cladding, and walls.C/Z Purlin Roll Forming Machine is a type of Roll Forming Machine that is designed specifically for producing C-shaped and Z-shaped purlins. These purlins are used for making pre-engineered steel buildings, industrial sheds, warehouses, and other structures. The machine works by feeding a strip of metal through a series of rollers that shape the metal into the desired profile. The final product is a strong, lightweight, and durable purlin that can withstand heavy loads and adverse weather conditions.Key Market Players in Automatic Roll Forming Machine MarketThe key market players in the Automatic Roll Forming Machine market include Bradbury Group, Framing Tech, Formtek Group, Gasparini Industries, HILALMAK, Howick, Isolaminas, JET USA, Knauer Engineering, L.B. Bohle Maschinen + Verfahren, M.Torres, Onward Machinery, PEP brainin, Taicang Keboer, TOX Pressotechnik, TRL Krosaki Refractories Limited, Xiamen Zheng Liming Metallurgical Machinery, and Yoder.Market SegmentationThe global Automatic Roll Forming Machine market can be segmented based on product type, application, and region.Based on Product Type, the market can be segmented into:• C/Z Purlin Roll Forming Machine• Corrugated Sheet Roll Forming Machine• Tile Roll Forming Machine• OthersBased on Application, the market can be segmented into:• Construction• Automotive• Electronics• Aerospace• OthersBased on Region, the market can be segmented into:• North America• Europe• Asia-Pacific• Middle East and Africa• South AmericaRegional AnalysisThe Asia-Pacific region is expected to dominate the Automatic Roll Forming Machine market in the forecast period, owing to the increasing demand for industrialization in countries such as China, India, and Japan. The region also has a large base of manufacturers and a significant consumer base for Roll Forming Machines. The North American and European markets are also expected to witness steady growth due to the increasing demand for lightweight and durable materials in the construction and automotive industries.ConclusionThe Automatic Roll Forming Machine market is expected to witness robust growth in the coming years, owing to the increasing demand for lightweight and durable materials in the construction, automotive, electronics, and aerospace industries. C/Z Purlin Roll Forming Machines are expected to witness significant demand, owing to the increasing demand for pre-engineered steel buildings, industrial sheds, and warehouses. The Asia-Pacific region is expected to dominate the market, owing to the increasing demand for industrialization in the region. The key market players in the market are Bradbury Group, Framing Tech, Formtek Group, Gasparini Industries, HILALMAK, among others.
Portable Standing Seam Metal Roof Roll Forming Machine: Small Size Standing Seam Roof Panel Roll Forming Machine
: A Game-Changer for the Metal Roofing IndustryMetal roofing has been gaining popularity over the years due to its durability, longevity, and aesthetic appeal. However, installing a metal roof comes with a fair amount of challenges, including finding a reliable and efficient roll forming machine that can produce the necessary roofing panels onsite. Enter the Portable Standing Seam Roll Forming Machine.The Portable Standing Seam Roll Forming Machine, also known as KLS25-220-530, is a small size metal standing seam roof panel roll forming machine that is designed to produce high-quality roof panels quickly and efficiently. It features a compact design, making it easy to transport and set up on-site, making it the perfect solution for contractors who need to produce standing seam metal roof panels on the job site.The machine is designed to roll-form metal roofing panels with a standing seam profile, which provides superior weather resistance and no visible fasteners. The standing seam design also makes it easier to install the panels, reducing the installation time and minimizing the risk of leaks.One of the standout features of the Portable Standing Seam Roll Forming Machine is its ease of use. It comes with an intuitive control system that allows operators to adjust the roll-forming settings quickly and easily. The machine also has a hydraulic cutting system, which cuts the panels to the desired length accurately.The KLS25-220-530 is capable of producing roofing panels with a width of 220mm and a thickness of 0.4-0.6mm. The machine also has a roll-forming speed of up to 15 meters per minute, ensuring that you can produce high-quality panels quickly and efficiently.Moreover, the machine comes with a durable construction, ensuring that it can withstand harsh job site conditions. It is also designed with safety features such as protective covers and emergency stop buttons, ensuring that operators are protected while using the machine.In conclusion, the Portable Standing Seam Roll Forming Machine is a game-changer for the metal roofing industry. Its portability, ease of use, and ability to produce high-quality standing seam metal roof panels quickly and efficiently make it an excellent investment for contractors looking to save time and money on their metal roofing projects. Don't wait any longer; invest in the KLS25-220-530 today.
Get High-Quality Glazed Tile Roof Panel Roll Forming Machines in Kenya
Glazed Tile Roof Panel Roll Forming Machine is a revolutionary creation in the roofing industry. Its introduction is a significant milestone in fulfilling the roofing needs of millions of people across the globe. This machine is designed to cater to all the demands of both commercial and residential buildings. The Glazed Tile Roof Panel Roll forming Machine is an exclusive production of (need remove brand name), which is a reputed manufacturer of high-quality roll forming machines.The (need remove brand name) has been committed to providing state-of-the-art equipment for the metalworking industry for decades. They are a globally renowned roll forming machine manufacturer, with an extensive network of customers in over 50 countries worldwide. They have a team of experienced professionals who are dedicated to designing, developing, and manufacturing high-quality roll forming machines. Their products are manufactured with precision, meeting the most stringent quality standards, and hence, the company has an excellent reputation in the market.The traditional roofing materials have been replaced by modern ones to provide better energy efficiency, aesthetics, and durability. Glazed Tile roofing panels have become increasingly popular in recent times due to their superior performance characteristics. These panels are made up of galvanized steel sheets, which are coated with several layers of paint to give them a glossy finish. The glazed tile roofing panels are perfect for commercial and residential buildings due to their insulation properties, durability, and lightweight.The Glazed Tile Roof Panel Roll Forming Machine is designed to produce perfect glazed tile roofing panels. The machine uses advanced technology that ensures that the produced panels have high precision and good quality. The roofing panels produced by this machine have an impressive lifespan, with the ability to resist all harsh weather conditions, including extreme heat, wind, and heavy rainfall.The Glazed Tile Roof Panel Roll Forming Machine is a fully automated machine that has been enhanced by modern technology to ensure high efficiency and productivity. The machine is designed with user-friendly features that enable the operator to produce high-quality products with ease. The machine’s automated control system ensures that the rollers automatically adjust their position based on the specifications provided, thus avoiding any manual interventions in the process.Moreover, the Glazed Tile Roof Panel Roll Forming Machine is designed to be reliable, durable, and easy to maintain. The company provides a comprehensive after-sales support service, which includes training and ongoing technical support, to ensure that clients always get the best results from their machines. Also, the machine is built with the latest technology, which ensures that its energy consumption is minimal.In conclusion, the Glazed Tile Roof Panel Roll Forming Machine is an innovative solution for roofing needs. Its introduction is a significant milestone in fulfilling the roofing demands of millions of people worldwide. The machine is designed to cater to both commercial and residential buildings' roofing needs. It is an exclusive production of (need remove brand name), which is a highly reputable and experienced manufacturer of roll forming machines. The Glazed Tile Roof Panel Roll Forming Machine is reliable, durable, and easy to maintain, and customers can count on its excellent quality and performance. The machine is a must-have for any business or individual seeking high-quality roofing solutions.
Pros and Cons of Corrugated Metal Roofing: Cost, Installation, and Benefits
If you're considering a new roof for your home or business, you might want to take a closer look at corrugated metal roofing. This type of roofing has become increasingly popular in recent years, thanks to its many advantages over traditional roofing materials like asphalt shingles or tile. In this blog post, we'll take a closer look at corrugated metal roofing, its pros and cons, and why you should consider it for your next roofing project.What is Corrugated Metal Roofing?Corrugated metal roofing is made from sheets of galvanized steel or aluminum that have been shaped into corrugated waves or ridges. These ridges are what give the roofing its distinctive look, as well as its strength and durability. The sheets are typically installed over a layer of insulation, which helps to keep your home or business warm in the winter and cool in the summer.Pros of Corrugated Metal RoofingThere are many reasons to choose corrugated metal roofing over other types of roofing materials. Here are just a few of the pros:Durability: Corrugated metal roofing is incredibly strong and durable, which means it can withstand harsh weather conditions like heavy rain, hail, and high winds. It's also resistant to fire, rot, and pests like termites.Longevity: Because of its durability, corrugated metal roofing can last for many years with minimal maintenance. In fact, many manufacturers offer warranties of up to 50 years on their roofing products.Energy Efficiency: Corrugated metal roofing is highly reflective, which means it can help to keep your home or business cool in the summer by reflecting the sun's rays away from your roof. This, in turn, can help to lower your energy bills and reduce your carbon footprint.Low Maintenance: Unlike other types of roofing materials, corrugated metal roofing requires very little maintenance. You don't need to worry about repairing or replacing shingles like you would with an asphalt roof, and you don't need to worry about moss or algae growth like you would with a tile roof.Cons of Corrugated Metal RoofingWhile there are many advantages to corrugated metal roofing, there are also a few disadvantages to consider. Here are some of the cons:Cost: Corrugated metal roofing can be more expensive than traditional roofing materials like asphalt shingles, although the cost has come down in recent years. However, when you consider the durability and longevity of corrugated metal roofing, it can actually save you money in the long run.Sound: Some people find that corrugated metal roofing is louder than other types of roofing materials when it rains or hails. However, this can be mitigated by installing a layer of insulation between the roofing and the building.Appearance: Corrugated metal roofing has a distinctive look that may not be to everyone's taste. However, there are many different styles and colors of corrugated metal roofing available, so you're sure to find something that matches your aesthetic preferences.Why You Should Consider Corrugated Metal RoofingThere are many reasons to consider corrugated metal roofing for your home or business. Here are just a few:Durability: Corrugated metal roofing is incredibly strong and durable, which means it can withstand harsh weather conditions and last for many years with minimal maintenance.Energy Efficiency: Corrugated metal roofing is highly reflective, which can help to lower your energy bills and reduce your carbon footprint.Low Maintenance: Corrugated metal roofing requires very little maintenance compared to other types of roofing materials.Appearance: Corrugated metal roofing has a distinctive look that can add character and visual interest to your home or business.If you're considering a new roof for your home or business, be sure to explore all of your options before making a decision. Corrugated metal roofing offers many advantages over other types of roofing materials, and it just might be the perfect choice for your next roofing project.Corrugated Roofing Sheet Forming MachineTo ensure your corrugated metal roofing is made to the highest quality and specifications, it's important to work with a manufacturer who uses a high-quality corrugated roofing sheet forming machine. This machine is designed to create perfectly shaped corrugations in the metal roofing sheet, which ensures a secure fit and superior durability. At Regan Industrial, we use only the best machinery and materials to create our corrugated metal roofing products, so you can be confident that you're getting the best possible product for your home or business.
Roll Forming Machines for Metal Roof and Drywall Studs and Track
If you are involved in the construction industry, you probably know how important it is to have the right equipment to get the job done quickly and efficiently. One of the most essential pieces of equipment that you need is a metal stud making machine.There are many different types of metal stud making machines on the market, but the most popular ones are those that are designed to produce high-quality metal studs and tracks used in drywall installation and house making. These machines are known for their precision, accuracy, and speed, making them the perfect tools for any construction project.One of the best things about metal stud making machines is that they are incredibly versatile. They can be used to produce a wide range of metal studs and tracks, including those made from steel, aluminum, and other metals. This means that you can use them for a variety of different projects, from small-scale jobs like installing a new drywall partition to large commercial construction projects.Metal stud making machines come in a range of sizes and configurations to meet the needs of different construction businesses. Some machines are designed to be portable, while others are more stationary. Some machines are designed to produce only metal studs, while others can produce both studs and tracks.To ensure that you are getting the best metal stud making machine for your needs, it is important to do your research and compare different models and brands. Look for a machine that is easy to use, has a high level of automation, and can produce high-quality metal studs quickly and efficiently.One popular brand of metal stud making machines is Alibaba. Their drywall stud roll forming machine is designed to produce high-quality studs and tracks for drywall installation and house framing. This machine is easy to operate and can produce metal studs and tracks in a range of different sizes and configurations.Another popular brand of metal stud making machine is Jobsite Roll Forming Equipment. Their machines are designed to produce metal studs and tracks for a range of different applications, including both residential and commercial construction projects. These machines are known for their precision and speed, making them the perfect choice for any construction business.In conclusion, if you are in the construction industry and looking to invest in a metal stud making machine, there are plenty of options to choose from. Whether you are looking for a portable machine or a more stationary model, there is sure to be a machine that fits your needs. Just be sure to do your research and compare different brands and models to find the best machine for your construction business.
Troubleshooting Common Problems with Portable Roof Panel Rollforming Machines
[Company Introduction: Portable Roof Panel Rollforming Machine]Portable Roof Panel Rollforming Machine is a leading manufacturer and supplier of innovative rollforming equipment. Our state-of-the-art machines are designed to provide efficient and high-quality production of roof panels for various applications. With a commitment to excellence and customer satisfaction, we have become a trusted name in the industry.Our portable roof panel rollforming machines are designed to be versatile and easy to use, making them perfect for on-site projects. These machines are capable of producing high-quality roof panels with precision and speed, ensuring that your projects are completed on time and to the highest standards.However, like any machinery, portable roof panel rollforming machines may experience common problems that can affect their performance. In this article, we will discuss the four most common issues that machine operators may encounter and provide troubleshooting tips to address these problems effectively.Problem 1: Material Feeding IssuesOne of the most common problems with portable roof panel rollforming machines is material feeding issues. This problem can lead to uneven panel formation and affect the overall quality of the roof panels. Material feeding issues are often caused by misalignment of the material guides or worn-out rollers.Solution: First, check the alignment of the material guides and adjust them if necessary. Ensure that the material is properly inserted into the machine and aligned with the guides. If the rollers are worn out, they should be replaced to ensure smooth material feeding.Problem 2: Uneven Panel FormationUneven panel formation is another common issue that can occur with portable roof panel rollforming machines. This problem can be caused by misalignment of the forming rollers or worn-out tooling. Uneven panel formation can result in panels with inconsistent dimensions or defects.Solution: Check the alignment of the forming rollers and adjust them if needed. Inspect the tooling for wear and replace any worn-out parts. Proper alignment and maintenance of the machine are crucial to achieving uniform panel formation.Problem 3: Machine JammingMachine jamming can occur when the material gets stuck inside the machine, preventing the rollforming process from continuing. This can be caused by material build-up, misalignment, or worn-out components. Machine jamming can lead to production delays and negatively impact the overall efficiency of the operation.Solution: Regularly inspect the machine for any material build-up and clean it if necessary. Check the alignment of the components, such as the rollers and guides, and adjust them if needed. Replace any worn-out or damaged parts that may contribute to the problem.Problem 4: Electrical MalfunctionsElectrical malfunctions can disrupt the operation of a portable roof panel rollforming machine. These issues can be caused by faulty wiring, loose connections, or damaged electrical components. Electrical malfunctions can lead to machine breakdowns and pose safety risks.Solution: Check the wiring and connections for any signs of damage or looseness. Ensure that all electrical components are functioning correctly. If you suspect an electrical malfunction, it is advisable to seek assistance from a qualified technician to resolve the issue safely and efficiently.ConclusionPortable roof panel rollforming machines are versatile and efficient solutions for on-site production of high-quality roof panels. However, machine operators may encounter common problems that can affect their performance. To address these issues effectively, it is essential to regularly inspect and maintain the machine, ensure proper alignment of components, and promptly address any malfunctions. With proper troubleshooting and maintenance, operators can ensure the smooth operation and longevity of their portable roof panel rollforming machines.